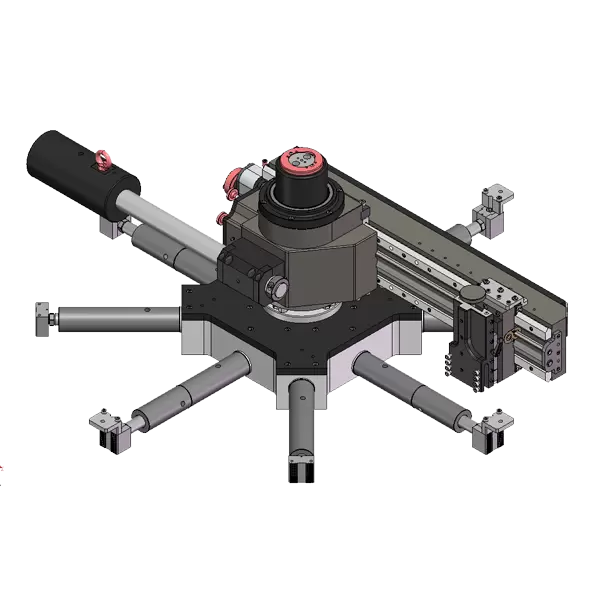
As an important precision mechanical equipment, flange facing machines are widely used in flange processing in the petroleum, chemical, metallurgy, electric power and other industries. Its main function is to process the flange end face to ensure the flatness and smoothness of the flange end face to meet the requirements of equipment installation and sealing. However, since the processing accuracy of the flange end face machine directly affects the quality of the flange and the safety of subsequent use, improving the processing accuracy of flange facing machines is an issue that every operator and equipment manufacturer must pay attention to.
This article will focus on how to improve the processing accuracy of the flange end face machine, explore the influencing factors and solutions in many aspects, and help improve the processing quality of flange facing machines.
1. The basic working principle of flange facing machines
Flange facing machines are usually used to process the end face of the flange to ensure the flatness and smoothness of the flange surface. The working principle of flange facing machines is relatively simple, basically cutting the flange end face through tool rotation or feeding device. The tool cuts along the surface of the flange end face to remove the uneven surface and achieve the required processing standards.
2. Factors affecting the machining accuracy of flange facing machines
The machining accuracy of flange end face machines is affected by many factors. The following are several main factors:
2.1 The accuracy of the equipment itself
The design and manufacturing accuracy of flange facing machines have an important influence on the machining accuracy. If the structure of the equipment itself is not rigid enough, or there are accuracy problems in the transmission system, it is difficult to ensure the machining accuracy. Therefore, it is crucial to choose a flange facing machine with a sturdy structure and stable accuracy.
2.2 Selection and configuration of tools
The role of tools in flange facing machines is very important. Suitable tools can effectively improve the machining accuracy. Common types of tools include high-speed steel tools, carbide tools, and coated tools. Choosing suitable tool materials and tool shapes can reduce tool wear, extend tool life, and thus improve machining accuracy.
2.3 Processing parameters
The processing parameters include cutting speed, feed rate, cutting depth, etc., which will directly affect the machining accuracy. Excessive cutting speed will cause increased tool wear, thereby affecting the machining accuracy; while excessive feed rate may cause the machining surface to be rough or vibrate. Therefore, it is necessary to reasonably adjust these parameters according to actual machining requirements.
2.4 Installation accuracy of flange end face
During the processing of flange facing machines, the installation accuracy of the flange is crucial to the final processing accuracy. If the installation position of the flange on the machine is inaccurate or the installation is not firm, it is easy to cause deviation during the processing. Therefore, it is very important to ensure the installation accuracy of the flange during processing.
2.5 Environmental factors
Environmental factors are also one of the important factors affecting the processing accuracy of flange facing machines. Temperature changes, humidity changes, dust and vibration in the environment may affect the processing accuracy of flange end face machines. Therefore, when operating flange facing machines, the working environment should be kept stable as much as possible to avoid unnecessary external interference.
3. Measures to improve the processing accuracy of flange facing machines
After understanding the factors affecting the processing accuracy of flange end face machines, we can improve its processing accuracy through the following aspects.
3.1 Choose high-precision flange facing machines
First of all, it is very important to choose a high-precision flange facing machine. High-precision equipment can provide a more stable processing environment and reduce processing errors during processing. For example, the use of higher rigidity, more stable mechanical structure, advanced automatic control system, etc. can effectively improve the machining accuracy of flange end facing machine.
3.2 Optimize tool selection and configuration
In the process of flange facing machines, it is very important to reasonably select tool materials and configuration. Carbide tools usually have better wear resistance and can maintain high stability in high temperature and high pressure processing environment, thereby improving machining accuracy. The cutting edge shape and angle of the tool should also be optimized according to specific processing requirements to achieve better cutting effect.
3.3 Accurate control of processing parameters
According to the characteristics of the processing material and the requirements of the workpiece, accurate control of processing parameters is another important measure to improve machining accuracy. For flange facing machine processing, it is usually necessary to reasonably set the cutting speed, feed rate and cutting depth according to factors such as the hardness and surface requirements of different materials. During the processing, the changes of these parameters need to be monitored in real time to ensure the machining accuracy.
3.4 Ensure the accuracy of flange installation
In the operation of flange facing machines, it is crucial to ensure that the flange is properly installed. The flange can be ensured to be stable and maintain the correct position during the processing by using special flange fixtures and fixtures. The higher the accuracy of the fixture, the higher the accuracy of the flange installation, thereby reducing processing errors and improving processing accuracy.
3.5 Regular maintenance and inspection of equipment
The processing accuracy of flange facing machines is also closely related to the maintenance status of the equipment. Regular inspection and maintenance of flange facing machines can timely discover potential problems of the equipment and repair them. For example, check and clean the transmission system, adjust the tool wear, check the electrical system, etc., to ensure that the equipment is always in the best working condition.
3.6 Control environmental factors
In order to reduce the impact of environmental factors on the processing accuracy of flange facing machines, measures can be taken to control temperature and humidity. For example, install temperature and humidity control equipment in the workshop to maintain a constant state of the environment. At the same time, the workshop should be kept clean to avoid dust and other substances affecting the processing quality.
3.7 Introduce high-precision testing equipment
In order to better monitor the processing accuracy of flange facing machines, some high-precision testing equipment can be introduced, such as three-coordinate measuring instruments, laser measuring instruments, etc. By real-time monitoring of each parameter in the processing process, the accuracy deviation can be discovered in time and adjusted to ensure the processing accuracy of the flange end machine.
Improving the machining accuracy of flange facing machines is a systematic project, involving equipment selection, tool configuration, machining parameter setting, flange installation, equipment maintenance and other aspects. By taking scientific and reasonable measures, the machining accuracy of flange end face machines can be significantly improved, and the quality of flange end faces can be ensured, thereby providing guarantees for subsequent equipment installation and safe operation. Both equipment manufacturers and operators should pay attention to these influencing factors in their daily work, continuously optimize the machining process, and improve the machining accuracy of flange facing machines.
As a flange facing machines dealer, choosing us will not only allow you to obtain high-precision flange facing machines, but also enjoy professional after-sales services, providing strong guarantees for your production process.
https://www.nodha.com/
NODHA Industrial Technology Wuxi Co., LTD