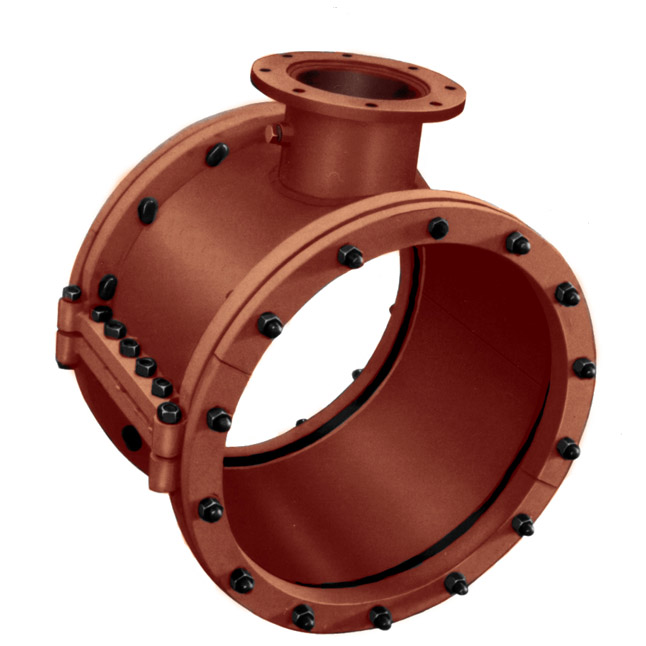
In the vast landscape of engineering, the question of whether joints can be welded or soldered is a nuanced inquiry that delves into the intricacies of material properties, structural requirements, and the intended applications. In this comprehensive exploration, we will navigate the complexities surrounding the feasibility of welding and soldering for joints, examining the processes, considerations, and scenarios where each method shines.
I. Welding Joints: Fusion at the Core
1. Understanding Welding:
Welding is a process that involves melting and fusing materials to create a strong, seamless connection. It is commonly used in structural applications where a permanent and robust joint is essential.
2. Types of Welded Joints:
Various types of welded joints exist, including butt joints, lap joints, and fillet joints. The selection of the welding technique depends on factors such as material thickness, joint configuration, and structural requirements.
II. Soldering Joints: The Art of Precision Bonding
1. Overview of Soldering:
Soldering is a process that uses a lower melting point filler material, known as solder, to join metals. It is often employed in electronics and applications where a lower-temperature, reversible joint is needed.
2. Soldered Joint Applications:
Soldering is prevalent in electronic circuits, plumbing connections, and delicate components where excessive heat could cause damage. It allows for precise and controlled bonding without compromising the integrity of the materials.
III. Considerations for Welding Joints: Strength and Stability
1. Material Compatibility:
Welding is most effective when joining similar materials. Compatibility in terms of metallurgical properties, melting points, and thermal expansion characteristics is crucial for achieving a strong and durable welded joint.
2. Structural Integrity:
Welded joints provide exceptional structural integrity, making them suitable for load-bearing applications. Engineers must ensure proper joint design, weld quality, and adherence to industry standards for optimal performance.
IV. Considerations for Soldering Joints: Delicate Precision
1. Material Selection:
Soldering is effective for joining materials with lower melting points, such as electronic components and thin metals. Careful consideration of material compatibility and solder alloy composition is vital for creating reliable soldered joints.
2. Reversibility:
One of the advantages of soldered joints is their reversibility. This makes soldering suitable for applications where components may need to be replaced or modified without causing damage to the surrounding materials.
V. Applications: Where Each Method Excels
1. Welding Applications:
Welding is indispensable in heavy industries such as construction, automotive manufacturing, and shipbuilding. It is the go-to method for creating permanent joints in structures and components subjected to high loads and stresses.
2. Soldering Applications:
Soldering finds its niche in electronics, jewelry making, plumbing, and delicate instrument assembly. Its ability to create precise, low-temperature joints makes it ideal for applications where preserving the integrity of sensitive materials is paramount.
VI. Challenges and Innovations: Advancing the Art of Joining
1. Welding Challenges:
Challenges in welding include distortion of materials, heat-affected zones, and the need for skilled labor. Innovations such as robotic welding and advanced welding techniques aim to address these challenges for improved efficiency and precision.
2. Soldering Innovations:
In the realm of soldering, innovations focus on lead-free solder alloys, automated soldering processes, and the integration of smart technologies. These advancements aim to enhance the reliability and efficiency of soldered joints.
VII. Conclusion: Crafting Connections with Precision
In conclusion, the feasibility of welding or soldering for joints depends on the specific requirements of the application, materials involved, and the desired permanence of the connection. Both methods have their strengths and applications, contributing to the intricate tapestry of engineering. This exploration serves as a guide for engineers and craftsmen navigating the art of crafting connections with precision, whether through the robust fusion of welding or the delicate bonding of soldering.