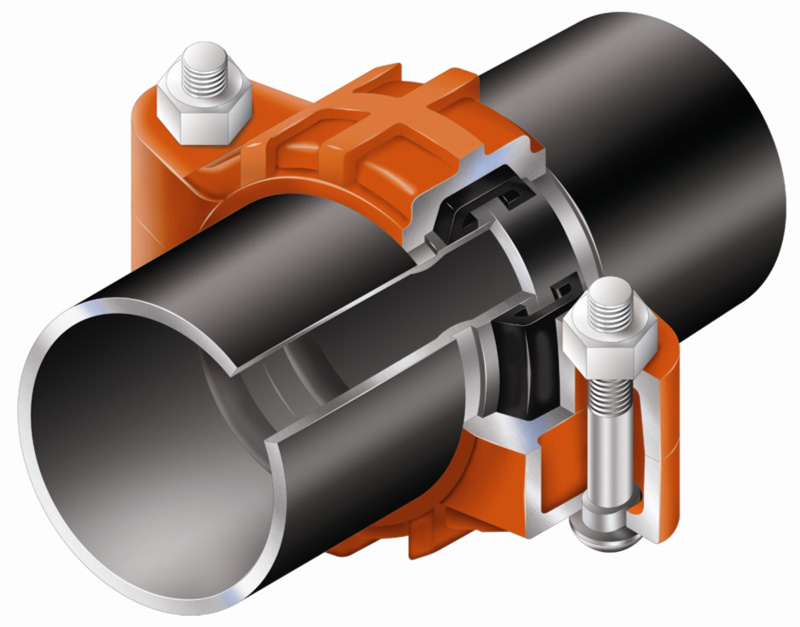
In the intricate world of engineering, the mechanical joint flange stands as a crucial element, facilitating connections in various industries with precision and reliability. This article delves into the depth of what a mechanical joint flange is, exploring its functions, applications, and the essential role it plays in ensuring seamless connections within complex systems.
I. Definition and Core Functionality:
A. Defining the Mechanical Joint Flange:
1. Integral Component in Piping Systems
2. Enabling Efficient Assembly and Disassembly
B. Key Functions:
1. Providing a Sealing Surface
2. Distributing Loads and Stresses
II. Types of Mechanical Joint Flanges:
A. Weld Neck Flanges:
1. Ideal for High-Pressure Applications
2. Enhanced Structural Integrity
B. Slip-On Flanges:
1. Easy Installation and Removal
2. Commonly Used in Low-Pressure Systems
C. Blind Flanges:
1. Closure of End Points in Piping
2. Applications in Isolation and Inspection
D. Lap Joint Flanges:
1. Unique Design for Swiveling Applications
2. Easy Alignment in Systems with Rotational Movement
III. Materials and Construction:
A. Material Selection:
1. Stainless Steel, Carbon Steel, and Alloy Options
2. Considerations for Corrosion Resistance
B. Manufacturing Processes:
1. Forging and Machining Techniques
2. Precision in Flange Dimensions
IV. Flange Faces and Sealing:
A. Raised Face Flanges:
1. Enhanced Gasket Compression
2. Common in High-Pressure Systems
B. Flat Face Flanges:
1. Easy Alignment and Installation
2. Suitable for Low-Pressure Applications
C. Ring-Type Joint (RTJ) Flanges:
1. Metal-to-Metal Sealing
2. High-Pressure and High-Temperature Environments
V. Standards and Regulations:
A. ASME B16.5 Standard:
1. Dimensions and Tolerances
2. Compliance with Industry Standards
B. Flange Ratings:
1. Pressure-Temperature Ratings
2. Matching Flange and Pipe Ratings
VI. Applications Across Industries:
A. Oil and Gas Sector:
1. Flanges in Pipeline Systems
2. Offshore and Onshore Applications
B. Chemical Processing:
1. Corrosion-Resistant Flange Materials
2. Ensuring Chemical Compatibility
C. Power Generation:
1. Flanges in Boiler Systems
2. High-Temperature Applications
VII. Installation and Maintenance Best Practices:
A. Proper Flange Alignment:
1. Avoiding Misalignment Issues
2. Impact on Sealing and Performance
B. Gasket Selection and Installation:
1. Compatibility with Fluids and Temperatures
2. Preventing Leakage and Ensuring Tight Seals
VIII. Innovations and Future Trends:
A. Smart Flanges:
1. IoT Integration for Monitoring
2. Predictive Maintenance in Industrial Systems
B. Sustainable Flange Materials:
1. Eco-Friendly Alternatives
2. Contributing to Green Engineering Practices
Conclusion:
In the intricate dance of engineering systems, the mechanical joint flange emerges as a choreographer, orchestrating seamless connections with precision. This article serves as a comprehensive guide, unraveling the complexities of mechanical joint flanges and emphasizing their critical role in fostering efficiency, reliability, and innovation within diverse industrial landscapes.